How IoT is Transforming the Manufacturing industry: Use Cases, Benefits and Trends in 2023 and beyond
In a world where innovation and efficiency are paramount, the manufacturing industry stands at the forefront of technological transformation. The Internet of Things (IoT) has emerged as a catalyst, reshaping the manufacturing landscape in unimaginable ways.
In this comprehensive article, we delve deep into the realms of IoT and its profound impact on the manufacturing sector. From its underlying technologies to real-world applications, benefits, challenges, and future trends, this article serves as your compass in navigating the IoT-driven manufacturing ecosystem in 2023 and beyond.
Table of content
- IoT: An attempt to bring Digital transformation into the manufacturing industry
- The Digital Transformation Imperative
- Why is IoT gaining traction in 2022 and beyond?
- Components of IoT
- How IoT is Transforming the Manufacturing Industry
- Benefits of IoT in manufacturing and related industries
- Challenges of IoT adoption in manufacturing and business
- Exciting IoT Use Cases in Manufacturing
- IoT Trends in Manufacturing for 2023
- Conclusion
- FAQ
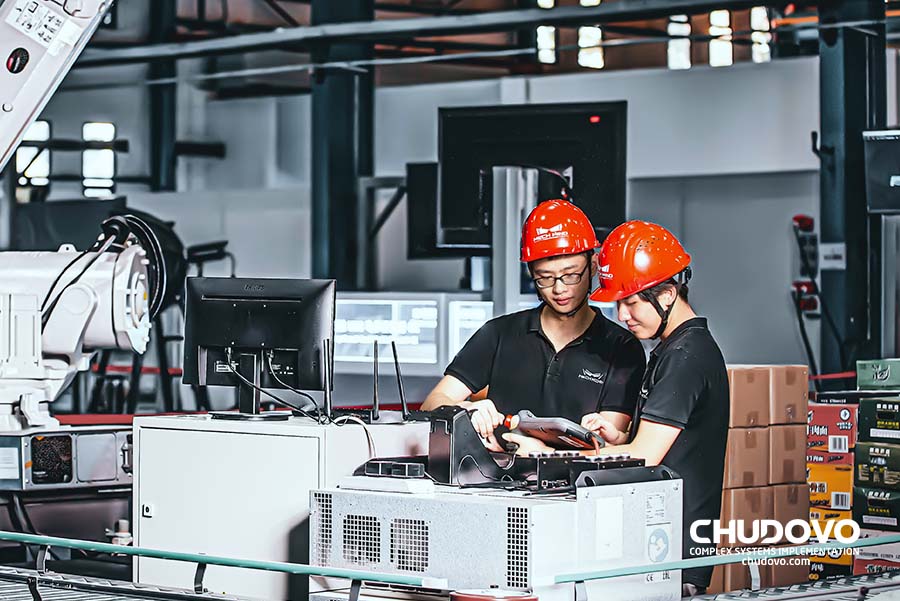
IoT: An Attempt to Bring Digital Transformation to the Manufacturing Industry
In the rapidly changing terrain of modern industry, the manufacturing sector has traditionally been characterized by its intricate processes, intricate machinery, and the meticulous orchestration of resources. Over the years, it has honed its expertise in producing goods at scale with unparalleled precision. Yet, despite its historical resilience and adaptability, the manufacturing industry finds itself at a crossroads in the 21st century, confronted by the imperatives of a rapidly changing digital age.
In the quest for greater efficiency, enhanced quality, and competitive advantage, manufacturers are embracing a transformative force that promises to reshape their very foundations: the Internet of Things (IoT). As we delve into the depths of this article, it becomes increasingly evident that the infusion of IoT technologies into the manufacturing ecosystem is far from a mere attempt—it is an unequivocal catalyst for a profound and comprehensive digital transformation.
The Digital Transformation Imperative
As we navigate the digital age, the manufacturing industry stands at the precipice of a transformational journey. This transformation is not just an option; it’s an imperative driven by several converging factors:
- Market Demands
In a global marketplace characterized by rapidly changing consumer preferences and demand for tailored products, manufacturers must adapt swiftly to remain competitive.
- Technological Advancements
The digital landscape is evolving at an unprecedented pace, offering manufacturers access to various enabling technologies, including IoT, artificial intelligence (AI), and big data analytics.
- Competitive Pressures
Rivalry within the manufacturing sector is fierce. Those who embrace digital transformation gain a distinct competitive advantage.
- Sustainability Goals
With increasing emphasis on sustainability, manufacturers must optimize resource utilization, reduce waste, and minimize environmental impact—objectives IoT can help achieve.
- Operational Efficiency
Efficiency is the linchpin of success in manufacturing. IoT-driven insights into operations enable manufacturers to streamline processes and reduce costs.
Here are some mind-boggling numbers and data about IOT and manufacturing worth paying attention to:
- A report by MarketsandMarkets forecasts that the global IoT in manufacturing market size is expected to grow from $33.2 billion in 2021 to $63.4 billion by 2026 at a compound annual growth rate (CAGR) of 13.8% during this period. This staggering growth indicates the industry’s recognition of IoT’s transformative potential.
- The World Economic Forum’s Digital Transformation Initiative notes that Industry 4.0 technologies, including IoT, can unlock up to $3.7 trillion in value for the manufacturing and supply chain industries by 2025.
- According to Deloitte, manufacturers already implementing IoT solutions have reported an average increase of 28.5% in operational efficiency.
As we dissect these figures, it becomes evident that IoT is not merely gaining traction but marching forward with unwavering momentum, on the cusp of unleashing a tidal wave of change in the manufacturing sector. Its role is not merely an attempt but a resolute drive towards a digital transformation that promises to redefine the very essence of manufacturing as we know it.
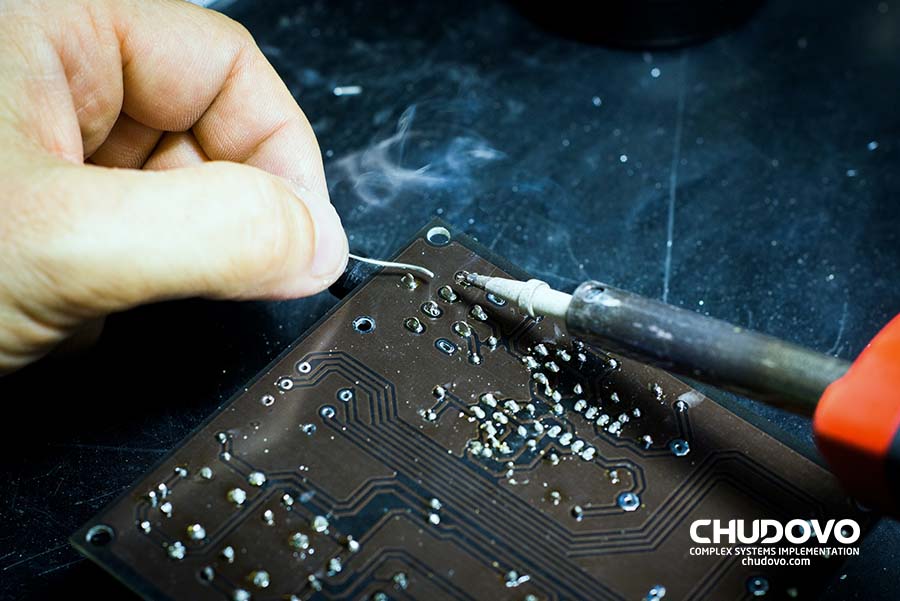
Why is IoT Gaining Traction in 2023 and Beyond?
IoT’s rise to prominence and traction within the manufacturing sector can be attributed to several converging factors, such as:
- Development of Smart Technologies: The proliferation of smart technologies has paved the way for IoT adoption, with sensors, actuators, and smart devices becoming more affordable and accessible.
Three Major Technologies Empower IoT and responsible for its traction
IoT’s transformative power stems from its integration with these three major technologies:
- 5G: The rollout of 5G networks is a game-changer for IoT in manufacturing. Its low latency and high bandwidth enable real-time data transmission and remote control of machinery.
- Artificial Intelligence (AI): AI-driven enterprise solutions have the potential to revolutionize manufacturing processes. Machine learning algorithms can analyze vast datasets, predict maintenance needs, and optimize production.
- Big Data: The vast amount of data IoT devices generate necessitates robust big data analytics. These insights drive efficiency, improve product quality, and optimize supply chains.
- Cost-Efficiency: IoT solutions have become more cost-effective, enabling manufacturers of all sizes to implement these technologies.
- Data-Driven Insights: The importance of data analytics cannot be overstated. IoT empowers manufacturers with real-time data insights, enabling informed decision-making.
- Competitive Edge: Staying ahead in the manufacturing industry requires innovation. IoT provides a competitive edge by improving efficiency, reducing downtime, and enhancing product quality.
Components of IoT
To comprehend the impact of IoT on manufacturing, it’s essential to understand its core components, which include:
- Sensors and Actuators: These devices collect data and trigger actions based on predefined criteria. Sensors monitor variables like temperature, pressure, and machine performance, while actuators control machinery and processes.
- Connectivity: Reliable communication protocols, including Wi-Fi, Bluetooth, and 5G, facilitate seamless data transfer between devices and systems.
- Cloud Computing: The cloud is a central hub for data storage, analysis, and access, making real-time insights available to stakeholders.
- Edge Computing: For applications requiring low latency, edge computing processes data locally on IoT devices, reducing latency and ensuring rapid response times.
How IoT is Transforming the Manufacturing Industry
IoT’s impact on manufacturing transcends the factory floor, permeating every facet of the industry. Here are some key ways IoT is driving transformation:
Predicts Early Malfunctions
One of IoT’s most significant contributions to manufacturing is predictive maintenance. Through continuous monitoring of machinery, sensors can detect early signs of wear and tear, enabling timely maintenance and reducing costly downtime. For example, automotive manufacturers can use IoT to predict when a machine in an assembly line might malfunction, preventing production delays.
Higher Margins and Customer Satisfaction Levels
IoT enables manufacturers to optimize their processes, reducing costs and increasing profit margins. Furthermore, by delivering high-quality products consistently, manufacturers enhance customer satisfaction, fostering brand loyalty. A classic example is the consumer electronics industry, where IoT-driven quality control ensures products meet stringent standards.
Improved Asset Management via Connected Supply Chain
IoT extends its reach beyond the factory floor, facilitating end-to-end supply chain management. Manufacturers can track the movement of raw materials, monitor storage conditions, and optimize logistics in real time. For instance, in the food industry, IoT sensors ensure the temperature and humidity of perishable goods remain within acceptable limits during transport, reducing spoilage.
Implements Operational Intelligence
Manufacturers leverage IoT to gain operational intelligence by collecting data from various sources, including production machinery, sensors, and employee interactions. AI algorithms analyze this data to identify bottlenecks, optimize workflows, and streamline operations. This approach has been instrumental in improving efficiency in the pharmaceutical manufacturing sector.
Boosts Quality
The quest for quality is a constant in manufacturing, and IoT assists by continuously monitoring production processes. Sensors detect deviations from established parameters, triggering immediate corrective actions. In aerospace manufacturing, for instance, IoT ensures precise measurements and adherence to stringent quality standards.
Improved Production Planning and Scheduling
IoT-driven data analytics enable manufacturers to fine-tune production schedules based on real-time demand and resource availability. The automotive industry, for instance, uses IoT to optimize production schedules, ensuring the right parts are available at the right time to meet customer orders.
Better Plant Safety and Security
Safety is paramount in manufacturing, and IoT enhances it by monitoring safety conditions and alerting personnel to potential hazards. For example, chemical manufacturing plants employ IoT sensors to detect leaks or unusual emissions, preventing accidents.

7 Benefits of IoT in Manufacturing and Related Industries
IoT brings many benefits that transcend the confines of the factory floor, extending its transformative influence into related industries and sectors. In this section, we will explore the myriad ways in which IoT empowers manufacturing and its adjacent domains. From cost efficiencies to sustainable practices, the advantages of IoT are as diverse as they are compelling.
Cost Reduction
At the heart of every successful manufacturing operation lies the pursuit of cost-effectiveness. IoT reigns as a beacon of hope in this endeavor. IoT solutions are instrumental in trimming operational expenses by enhancing resource allocation, reducing downtime through predictive maintenance, and optimizing energy consumption. For instance, a study by Capgemini found that manufacturers adopting IoT achieved a 15% reduction in maintenance costs.
Enhanced Product Quality
In the competitive manufacturing world, quality is paramount. IoT-equipped sensors and real-time monitoring systems ensure consistency in product quality by identifying deviations from established standards. This quality assurance reduces waste and bolsters a manufacturer’s reputation. For example, automotive manufacturers employ IoT to ensure precise measurements and adherence to stringent quality standards, minimizing defects and recalls.
Efficient Supply Chain Management
The tentacles of IoT extend far beyond the factory walls, permeating the entire supply chain. Manufacturers can optimize logistics, minimize spoilage, and ensure timely deliveries by facilitating real-time tracking and monitoring of goods in transit. A prime illustration is the food industry, where IoT sensors maintain the desired temperature and humidity levels for perishable goods, preserving their integrity during transportation.
Predictive Maintenance
Predictive maintenance is one of IoT’s most compelling manufacturing advantages. IoT sensors detect early signs of wear and tear through continuous monitoring of machinery and equipment, enabling proactive maintenance. This extends the machinery’s lifespan and minimizes costly production disruptions. For instance, automotive manufacturers can predict when a machine on the assembly line might malfunction, averting production delays.
Improved Decision-Making
In the digital age, data reigns supreme. IoT furnishes manufacturers with a continuous stream of real-time data and analytics. These insights empower decision-makers at all levels of the organization, from shop floor supervisors to C-suite executives, enabling data-driven choices. With the right data at their fingertips, manufacturers can optimize processes, allocate resources effectively, and adapt swiftly to market fluctuations.
Competitive Advantage
In a cutthroat manufacturing landscape, staying ahead of the competition is the key to survival. IoT adoption provides a critical competitive edge. It enhances efficiency, reduces downtime, and consistently ensures that products meet the highest quality standards. Manufacturers embracing IoT are not just keeping pace but setting new industry standards. This competitive edge is particularly evident in industries like consumer electronics, where IoT-driven quality control ensures products meet stringent standards.
Energy Efficiency
Energy costs constitute a significant portion of a manufacturer’s operational expenses. IoT plays a pivotal role in optimizing energy consumption. Through smart sensors and real-time monitoring, manufacturers can identify and rectify inefficiencies in their energy usage, leading to substantial cost savings. For instance, IoT-driven solutions help factories minimize energy wastage by automatically adjusting lighting and HVAC systems based on occupancy and environmental conditions.
The aforementioned benefits are clear, tangible, and transformative, making IoT adoption an imperative for manufacturers looking to remain at the forefront of innovation and excellence.
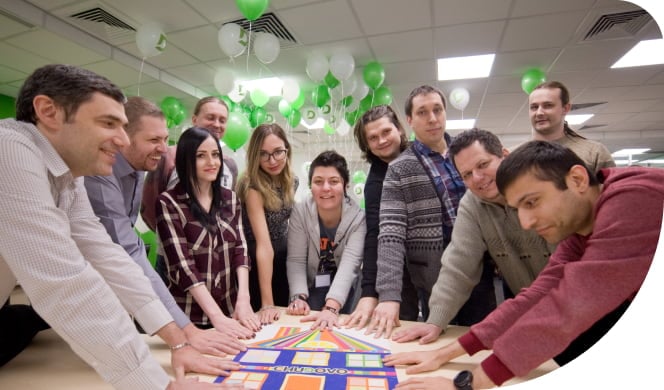
Certified engineers
Convenient rates
Fast start
Profitable conditions
Agreement with
EU company
English and German
speaking engineers
5 Challenges of IoT Adoption in Manufacturing and Business
In this section, we dissect the five pivotal challenges businesses face when embracing IoT in manufacturing and delve into strategies and insights to navigate these hurdles effectively.
Cost of Implementation
The initial investment required for IoT implementation can be substantial. The financial burden can be daunting for small and mid-sized manufacturers, from acquiring IoT sensors and devices to overhauling existing infrastructure and ensuring cybersecurity. Addressing this challenge necessitates careful budget allocation and long-term strategic planning. Companies must evaluate the return on investment (ROI) over time, weighing the potential cost savings and operational efficiencies IoT can deliver against the upfront expenses.
Data Security Concerns
With the proliferation of connected devices and the vast amount of data they generate, data security has become paramount. Manufacturers must safeguard sensitive information from cyber threats, ensuring data privacy and integrity. Effective cybersecurity measures are indispensable, including encryption, intrusion detection systems, and regular vulnerability assessments. Moreover, fostering a culture of cybersecurity awareness among employees is critical to mitigate risks effectively.
Interoperability Issues
The manufacturing landscape has legacy systems and heterogeneous devices. Integrating IoT seamlessly with these existing technologies can be a formidable challenge. Achieving interoperability often requires developing custom solutions or middleware to bridge the gaps between different systems. It’s essential for manufacturers to assess their current infrastructure, define clear integration strategies, and work closely with technology partners to ensure a smooth transition.
Talent Gap
Leveraging IoT technology effectively demands a skilled workforce with data analytics, IoT architecture, and cybersecurity expertise. The shortage of professionals with these specialized skills poses a significant challenge. Companies must invest in training and upskilling their existing workforce while actively recruiting talent versed in IoT technologies. Collaborating with educational institutions and fostering partnerships with IoT-focused training programs can help bridge the talent gap.
Scalability Challenges
As manufacturing businesses grow, their IoT solutions must evolve and scale accordingly. IoT deployments that work well for small-scale operations may not suffice for larger enterprises. Scaling IoT systems involves careful planning to ensure that the infrastructure can accommodate increased data volumes and device connectivity. Manufacturers should adopt a modular approach to IoT implementation, allowing for seamless scalability as their operations expand.
The challenges of IoT adoption in manufacturing and business are formidable, but they are by no means insurmountable. In the quest for greater efficiency, competitiveness, and innovation, these hurdles are akin to stepping stones toward digital transformation.
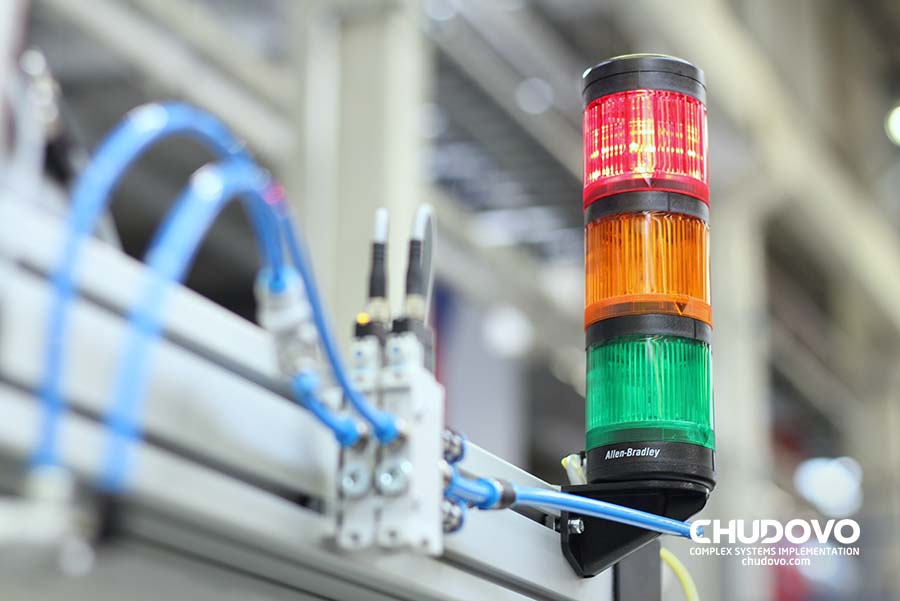
Exciting IoT Use Cases in Manufacturing
The world of manufacturing is undergoing a seismic transformation, and at the epicenter of this revolution is the Internet of Things (IoT). While the concept of IoT is captivating in its own right, it is the real-world applications that truly bring its potential to life. Here, we delve deep into the realm of IoT’s captivating use cases within the manufacturing sector.
Remote Monitoring
At the heart of IoT’s influence in manufacturing lies remote monitoring, an application with far-reaching implications. Manufacturers can now monitor their equipment, machinery, and processes in real time, irrespective of geographical distances.
For example, General Electric (GE) Aviation employs IoT sensors to oversee the performance of aircraft engines from a central location. This enables proactive maintenance, reduces downtime, and ensures optimal engine performance throughout its lifecycle.
Logistics Management
Logistics is the circulatory system of manufacturing, and IoT is a powerful optimizer. By integrating IoT into logistics management, manufacturers can revolutionize route planning, reduce delivery times, and enhance overall efficiency.
DHL, a global logistics leader, utilizes IoT-driven tracking and monitoring solutions to ensure the seamless flow of goods worldwide. These solutions enable precise real-time tracking and route optimization, ensuring timely deliveries while reducing operational costs.
Digital Twins
The concept of digital twins has taken IoT to a new level. A digital twin is a virtual replica of a physical object or process. In manufacturing, this technology allows for real-time simulation, analysis, and optimization of operations.
A renowned manufacturing giant, Siemens leverages digital twins to simulate entire factories, facilitating rapid prototyping, process optimization, and proactive issue resolution. This application of IoT saves both time and resources, enabling manufacturers to innovate faster.
Manufacturing Key Performance Indicators (KPIs)
Monitoring and optimizing manufacturing KPIs are essential for success. IoT equips manufacturers with real-time tools to track these KPIs, providing actionable insights.
Companies like General Motors employ IoT to monitor production line efficiency. This enables real-time performance assessment, ensuring that production targets are met, and resources are utilized optimally.
From remote monitoring that spans continents to logistics management that streamlines global supply chains, from the virtual realms of digital twins to the precision of manufacturing KPI monitoring, IoT catalyzes manufacturing into a future where innovation knows no bounds.
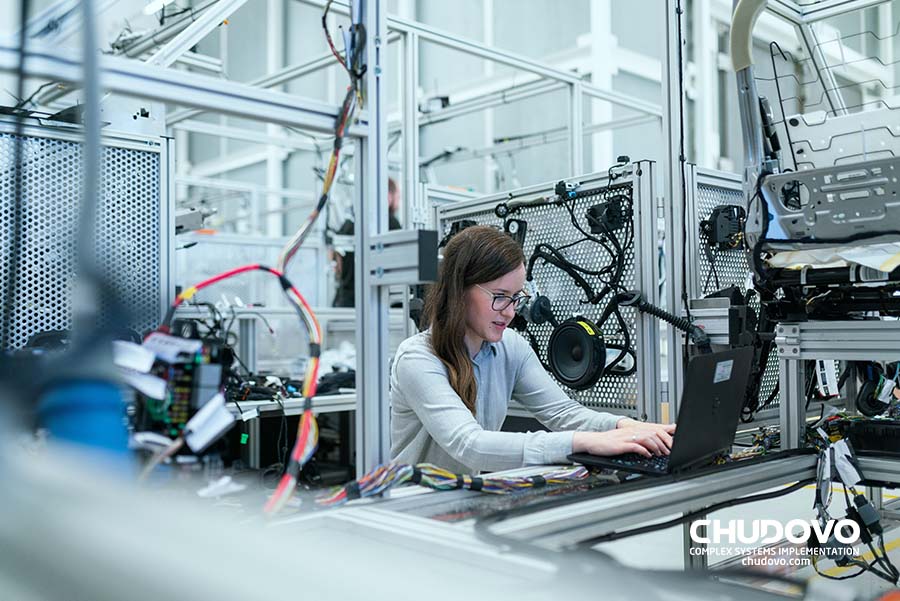
IoT Trends in Manufacturing for 2023
As we move further into the digital age, several IoT trends are set to shape the manufacturing landscape:
- AI-Driven Enterprise Solutions: Integrating AI and IoT will become more prevalent, offering advanced analytics and predictive capabilities.
- Custom IoT Solutions: Manufacturers will increasingly adopt custom IoT solutions tailored to their specific needs, such as custom software for manufacturing.
- Greater Focus on Data Security: Manufacturers will prioritize robust cybersecurity measures as data becomes more valuable.
- Industrial Internet Platforms: Platforms integrating various IoT solutions will gain prominence, simplifying management and scalability.
- Expansion into New Sectors: IoT’s influence will extend into traditionally non-digital sectors, such as agriculture and construction.
Conclusion
The Internet of Things is reshaping the manufacturing industry, bringing about a new era of efficiency, quality, and innovation. In 2023 and beyond, IoT will continue to drive digital transformation, offering manufacturers a competitive edge and delivering benefits across the entire supply chain. As challenges are overcome and trends evolve, IoT’s role in manufacturing will only grow, cementing its status as a cornerstone of modern industrialization.
FAQ
What are the primary technologies powering IoT in manufacturing?
The primary technologies empowering IoT in manufacturing are 5G, Artificial Intelligence (AI), and Big Data.
How does IoT benefit manufacturing companies?
IoT benefits manufacturing companies by reducing costs, enhancing product quality, optimizing supply chain management, enabling predictive maintenance, improving decision-making, providing a competitive advantage, increasing energy efficiency, and contributing to sustainability.
What are the main challenges of IoT adoption in manufacturing?
The main challenges of IoT adoption in manufacturing include the cost of implementation, data security concerns, interoperability issues, the talent gap, and scalability challenges.
What are some exciting IoT use cases in manufacturing?
Exciting IoT use cases in manufacturing include remote monitoring, logistics management, digital twins, and real-time tracking of manufacturing KPIs.
To harness the full potential of IoT for your manufacturing business, consider partnering with Chudovo. With our expertise in custom Internet of Things solutions and AI-driven enterprise solutions, we can help you embark on a transformative journey toward greater efficiency, quality, and competitiveness. Contact us today to discuss your IoT needs.