Smarter Production Lines: The Rise of Machine Learning in Manufacturing
Many operations in the manufacturing industry are now being powered by machine learning, this solution transforms and boosts productivity, making them faster and more efficient. It redefines processes that involve human effort with the use of data.
Table of Contents
What is Machine Learning in manufacturing?
Computers are given certain instructions utilizing data so that they can learn and make predictions based on the insight gained. This process is called Machine learning. For instance, instead of explicitly instructing a machine-learning model on how to identify a dog, you feed the model with numerous images of a dog and images without a dog. Through repetition, this model understands what attributes have to exist in the available data for an object to be precisely categorized as a dog. The manufacturing industries are becoming more dependent on machine learning because its model can learn from the data given and use this to determine and predict results with precision.
By Leveraging machine learning in manufacturing users can better understand their production procedures. For example, some manual activities in production consume several hours to get done, such as sorting specific materials or items suitable for production. Such activity can be automated and achieved in less time.
Depending on the extent of the production issue and the volume of the data collected, root cause analysis is a technique that can help pinpoint the exact cause of a problem or failed test in production procedures. Machine learning will evaluate which of these causes still needs a human review. Hence, it reduces the amount of time expended on doing this analysis.
Putting together the insights acquired through integrating machine learning into procedures for manufacturing industries will not only fix production-related issues but will completely remove the problem. For instance, the machine learning model can propose which parts of manufacturing equipment should be coupled with other parts through the identification of crucial spots during installation so that you can properly prevent product defects. This is a very effective approach that reduces the repair of axle components.
One of the major importance of machine learning in manufacturing is how precisely it solves problems based on the information gained from it. Manufacturing organizations can decrease the rate of repairs and waste, enhance the quality of their product, and boost production efficiency through accurate data using machine learning strategies.
Based on the report from Statista, the amount of money invested in machine learning and artificial intelligence keeps increasing across all industries because of how effective these solutions are to various sectors. It was reported that in 2020, 83% of companies increased their budget on this solution compared to the previous year.
Think of a production facility where machines such as robots can predict the quality of products. That is one of the efficiencies of machine learning in end-of-line testing. for example, in complex components like engines, this solution redefines how it works because there is no need to check for every unit since machine learning is used to find potential defects before they happen. This ensures that high-quality products are delivered to customers and it saves production time.
Aspects of Machine learning implemented in manufacturing
Machine learning utilizes a range of techniques to tackle challenges. These techniques are often divided into two distinct types according to how the models learn. The method of learning that a technique uses can be assessed by the way it takes in data. These techniques are supervised and unsupervised learning.
Supervised machine learning
In the industrial setting, supervised learning is the most used approach because it ultimately results in a predetermined goal. In this approach, there are input data and output data; these two variables are related, and in order to establish that relationship, we use a function. This approach requires an extensive level of engagement which includes data input, design definition, data training, and presentation of data. The aim is to create a precise mapping function that enables us to forecast results when new input data is supplied to the model.
In this method, the model is trained with some sets of data that continuously enhance its efficiency and attempt to accomplish the outcome it wants. The procedures of learning finish once the model attains a satisfactory degree of correctness. The two most prevalent methods of supervised learning in manufacturing are:
Regression and Classification
Both of these approaches have a common objective: to create a connection between input data gotten from the process of production, and the output data which is the potential result. Examples of these potential results are component failure, wastage, and overheating.
- Regression
When data fits between a particular range such as temperature, or weight, which is the situation when utilizing sensor data – the results of a tool that senses and responds to certain types of inputs from the external environment. Regression is utilized in this case. In the manufacturing industry, regression can be applied to forecast a products remaining useful life. This is a projection of the number of days left until the components fails.
- Classification
This can be helpful when data has been structured into distinct categories. For example, the email filter algorithm is used to determine if an email is supposed to be directed to the spam folder or actual mail inbox. Classification is confined to a true or false value reply, yet it is very useful because just the right amount of data is necessary to obtain a substantial degree of precision.
Unsupervised learning
We usually start by evaluating our desired result in supervised learning and then train the model to perform correctly. However, for situations where the result is unknown, unsupervised learning is the suitable approach. There are two common categories of unsupervised learning:
- Clustering
In certain instances, the results will not only be unknown, but the details about the data will be insufficient Machine learning models can identify fundamental trends by combining incoming data points on particular features. Clustering can be used to minimize noise i.e. insignificant factors in data when working with excessive amount of variable.
- Artificial neural networks
This method has proven to be a very effective tool in unsupervised learning for the manufacturing industry. Its implementation includes manufacturing procedure simulation and predictive quality analytics. The key components of artificial neural networks are somewhat built based on how the brain of a human analyzes information, making use of its network of billions of neurons which enables comprehensive problem-solving.
Artificial neural networks are suitable for manufacturing procedures that make use of large amounts of variables and that change continuously because of their capability to handle an extensive amount of different variables over multiple layers. If this model is accurately and appropriately trained, it can produce a reliable prediction about the mechanical attributes of goods that are produced which enables reduction in expenditure of unprocessed products.
The Merits of Machine Learning in the Manufacturing Industry
Machine learning signifies an important turning point with numerous benefits that give rise to positive outcomes beyond just improved productivity in manufacturing. Its advantages in manufacturing procedures include:
- In order to continuously improve product quality, this solution is implemented with practical insights.
- Better management of the supply chain through the implementation of successful inventory control and a well-coordinated manufacturing procedure.
- Predictive maintenance reduces costs. It reduces operations related to maintenance which leads to lower labor expenses, and waste of material and stocks.
- Improved productivity through the enhancement of manufacturing procedures.
- Applying the approach of predicting remaining useful life which enables understanding the way machines and equipment work in manufacturing in order to set up conditions that boost its performance while preserving the efficiency of the machine.
- Productivity is enhanced, and the safety of staff is improved with the collaboration with human-robot built and trained with machine learning models
- With machine learning in the production industry can adjust swiftly to changes in consumer demands.
Application of Machine Learning in Manufacturing
The purpose of machine learning in manufacturing is to optimize production procedures with the efficient use of data. To be able to leverage machine learning, you must first have the capacity to evaluate the most suitable data points with the goal of determining enhancement in performance. With machine, learning manufacturing industries analyze large quantities of data more rapidly and effectively than humans can possibly achieve. Leveraging machine learning will help production companies evaluate the reliability and efficiency of all their equipment which makes predictive maintenance possible and successful because it determines the ideal time for servicing certain equipment with the objective of further increasing the lifespan and preventing downtime that leads to loss in revenue.
A recent study from Statista shows that Asia is the leading figure in the adoption of machine learning. The Asian market for this solution was valued at around 30 billion dollars, making it the largest in the world. North America and Europe were also in the picture, they have a value close to 20 billion dollars.
Enhancement in production
Machine learning helps manufacturing industries detect defects in their method of production. In each method of production, there is an assigned step with a variety of options that may be modified during the production procedure. Companies can detect production steps or procedures that are ineffective and modify them appropriately by reviewing large amounts of data for manufacturing using machine learning. Supply chains have connections with production, so machine learning technologies are used as influencing elements for smart supply chains that are developed in the current manufacturing sector. This enhances processes like warehouse control because goods can be restocked quickly with the help of inventory management leveraging machine learning algorithms. The most suitable transportation and delivery routes are identified easily because this solution is implemented in the transportation and logistics aspects of production.
Quality control
With the implementation of computer vision and machine learning into quality control systems, every aspect of the production procedure is automated and enhanced significantly. Because manufacturers know precisely what the finished product ought to be and they also have sufficient data to train their machine learning model. One of the most important aspects of machine learning in manufacturing is quality control. Automated suggestions and signals are created to inform production teams of an imminent challenge and to easily convey crucial details on how to avoid losses earlier than they occur.
Predictive maintenance
Maintenance of machinery is a vital process in production and it should be carried out periodically by experts in the field. manual technique is partially successful, but it has the drawback of unforeseen breakdowns of equipment which leads to an interruption in production operations and loss in earnings. for example, if equipment used in production is not identified earlier as faulty and it is used it can fail during its usage, thereby disrupting that process of production. Manufacturers can track the status of equipment and take preventive measures through the implementation of machine learning solutions. There are sensors installed to capture data from industrial equipment parts and transmit it to machine learning-based analytics designs that identify anomalies in performance and forecast the remaining useful life of the equipment and when it will break.
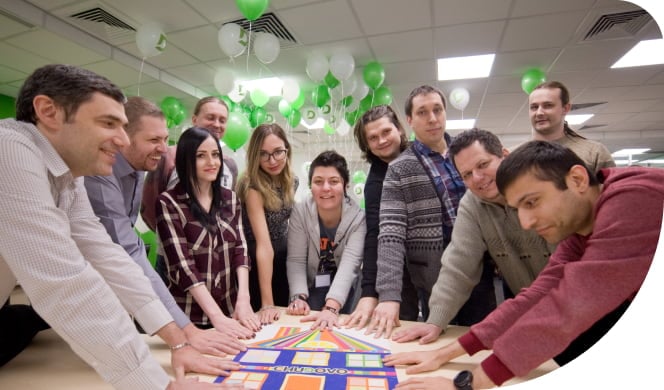
Certified engineers
Convenient rates
Fast start
Profitable conditions
Agreement with
EU company
English and German
speaking engineers
Steps in developing machine learning model in manufacturing
1. Give a meaning to the issue
- Evaluate the production procedure
It is important to have an adequate grasp of the method of production, the available data, and the particular difficulties you will want the machine learning model to tackle.
- Define specific targets
Establish the project accomplishments standard, including key performance indicators that will need to be enhanced.
2. Gather and organize the data needed
- Data collection
Obtain both historical and current information needed from the production procedure.
- Data cleaning
Because manufacturing industry collects data from multiple source for produtions procedures, It must be cleaned and all duplicated data points must be wiped out.
- Data translation
Machine learning algorithms are only able to handle values that are numerical non-numerical attributes such as strings must be interpreted and presented numerically.
- Picking of features and engineering
Determine the most significant element, which is the data inputs that influence the result you want to achieve. Develop extra features from the current data sets to enhance the effectiveness of the model.
3. Select a machine learning algorithm.
- Research algorithm
Choose a suitable machine learning algorithm for the type of problem you are trying to solve. For example clustering, classification, regression all of these are possible algorithms in machine learning that implemented in solving production-related problems.
- Consideration
Evaluate the technical difficulty of the problem, the resources needed for computation, and the kind of data to be used in building an efficient model.
4. Train the model.
- Split your data
It is vital you split your data into training and testing sets in order to evaluate the efficiency of the model. For instance, while developing a machine learning model that solves predictive maintenance challenges, the order of time is very important. Hence, the datasets must be properly distinguished. However, if the problem is about classification, such as identifying between defective and non-defective components, the order of time here is irrelevant. The dataset used for training and testing ought to contain an equal number of non-defective and defective components.
- Model training
With the use of the training data, give instructions to the model to give predictions based on the data provided. In the manufacturing industry, the problems often encountered are categorized into two: classification, such as pass vs fail for an end-of-line test, and regression.
5. Fine-tune and enhance the model
- Try out various values for the parameters associated with the model to figure out which of these will better produce an effective result.
- Based on the performance of a model, consider changing, eliminating, and introducing new features. Given that every instance is distinctive machine learning model has to be changed and tailored to get the most ideal outcome.
6. Assessment
- Real-time assessment.
Build machine learning models by feeding the algorithm with actual data after proper evaluation, cleaning, and structuring. These models perform on the insight of the data.
FAQ
What is the importance of machine learning in manufacturing?
This solution helps the manufacturing industry to solve problems based on the data gathered because when correct and appropriate data is utilized in training a model. it helps to enhance the entirety of production effectiveness.
What distinguishes supervised learning from unsupervised learning?
While the supervised learning algorithm uses labeled data which gives an insight on what the final result would be, unsupervised learning uses unlabeled data because the model learns on its own so that it can provide a final result in the case the final result is not known.
Why use machine learning in manufacturing?
The use of machine learning in the process of production enhances productivity. An approach like end-of-line testing utilizes machine learning to test for the quality of a product.
Contact the expert team of Chudovo software engineers to implement a machine-learning algorithm into your manufacturing process.