Streamline Your Manufacturing Operations with Modern Software Solutions
In the past, industries primarily relied on manual labor and rudimentary machines to manage their production processes. From manual operations logging to relying heavily on human decision-making, the manufacturing domain had its share of inefficiencies and challenges. However, as technology advanced, so did the tools available to these industries. Among these advancements, the emergence and growth of manufacturing software have been transformational.
- What Benefits of Production Management Software?
- How Manufacturing Software Impacts Industries?
- How Software Solutions Brings Workflow Automation Efficiency?
- What Legacy Software Modernization’s Significance?
- What are Management Benefits from Software Solutions?
- What is Data Analytics and Business Intelligence?
- How to Conduct Production Planning?
- Real-World CHUDOVO Project
- Conclusion
- FAQ
What Benefits of Production Management Software?
The world of manufacturing has always been competitive. From the early days of mechanized production lines to today’s technologically advanced factories, manufacturers have continually sought ways to enhance efficiency, reduce costs, and deliver superior products. In today’s digital age, Production Management Software (PMS) has emerged as a pivotal tool to achieve these goals.
To answer this, we need to look at the dynamics of the contemporary industrial landscape:
- Rapidly Evolving Consumer Demands: Modern consumers, equipped with instant access to information, demand high-quality products delivered quickly and tailored to their specific needs. PMS allows for rapid modifications to production lines, adapting swiftly to these changing requirements.
- Global Supply Chains: Many companies source materials and sell products globally. This introduces challenges in coordination, logistics, and inventory management. A robust PMS can integrate with supply chain systems, ensuring timely material availability and product dispatch, mitigating the risk of delays and stock-outs.
- Sustainability and Compliance: Increasing awareness of environmental concerns and stringent regulations necessitate that industries adopt sustainable practices. PMS assists businesses in monitoring energy consumption and waste production and ensuring adherence to environmental standards.
- Data-driven Decision Making: Data is the new oil. Companies that can efficiently harness their data can gain insights, predict trends, and optimize operations. PMS solutions have data analytics capabilities, turning raw data into actionable intelligence.
Centralized Monitoring and Control
As the industrial sectors grow more complex and interconnected, a centralized MES (Manufacturing Execution System) to monitor and control manufacturing processes becomes vital. With centralized control, managers can avoid manually synchronizing various departments, machinery, and personnel. A slip in any part can result in inefficiencies, wastage, and decreased output. PMS offers a unified dashboard, providing a glance overview of the production process, ensuring harmony and synchronization across the board.
Tools for Competitive Advantage
- Cost Reduction: One of the primary advantages of PMS is its potential for significant cost savings. Companies can markedly reduce production costs by optimizing resource allocation, reducing waste, and enhancing equipment efficiency, leading to healthier profit margins.
- Factory Automation: Modern PMS solutions often integrate seamlessly with factory automation systems. Automated machinery, guided by the software, can operate at peak efficiency, reduce human error, and enhance production speeds. This not only boosts output but also ensures consistency in product quality.
- Real-time Monitoring and Predictive Maintenance: PMS can monitor machinery health in real-time with sensors and Internet of Things (IoT) devices. Predictive maintenance algorithms can foresee potential breakdowns, allowing for proactive maintenance, reducing downtimes, and ensuring continuous production flow.
- Quality Assurance: PMS can integrate with quality assurance systems, conducting automatic checks throughout production. This ensures products meet the desired standards consistently, reducing the chances of defects and returns.
- Employee Management: Beyond machinery and processes, PMS can also assist in managing the workforce. Scheduling, task allocation, and performance tracking ensure that human resources are optimally utilized.
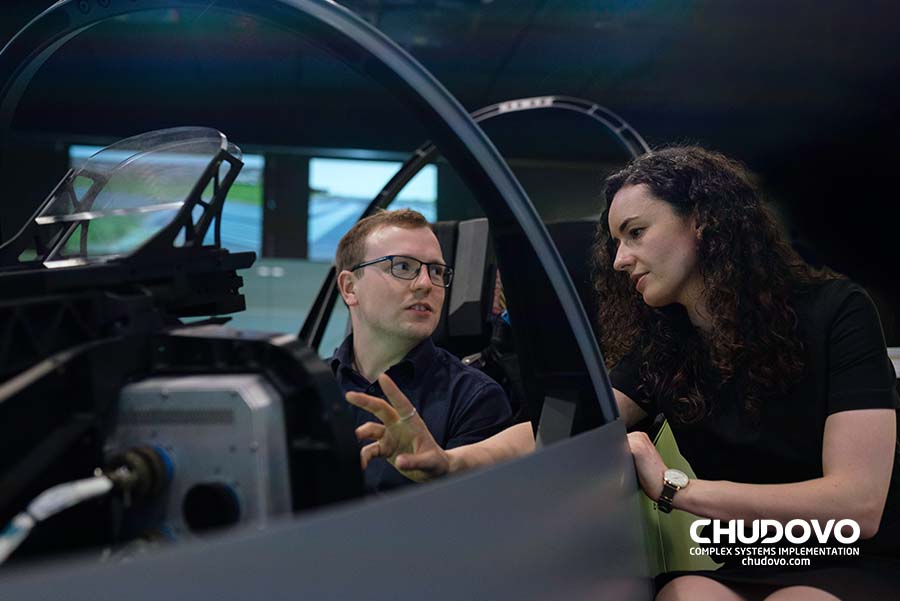
How Manufacturing Software Impacts Industries?
The dawn of the digital age has brought about a revolution beyond personal computing or communications. From its humble beginnings with manual labor and rudimentary machines, the industrial landscape is today at the forefront of this technological wave. Manufacturing software, a symbol of this change, has dramatically altered how industries operate. Let’s delve deeper into its impact across various sectors.
Textiles: The Fabric of Change
In the textile industry, precision, consistency, and speed are of the essence. Manufacturing software has enabled these factories to monitor every aspect of production, from the raw cotton processing to the final garment stitching. Automated dyeing processes, for instance, ensure consistent color quality across batches. On the other hand, predictive analytics can foresee equipment failures, ensuring that looms and knitting machines run optimally, reducing wastage and ensuring consistent output. With enhanced inventory management, manufacturers can keep track of raw materials, guaranteeing timely reorders and optimizing storage costs.
Aerospace: Soaring with Precision
A sector as critical as aerospace demands nothing short of perfection. A minor error can result in catastrophic consequences. Manufacturing software in this industry ensures that each component, often comprising thousands of parts, is built to exact specifications. From real-time monitoring of machinery calibrations to providing the precise alloy mixtures in metals, these systems ensure reliability and safety. Moreover, with supply chain optimization, these companies can manage their global suppliers efficiently, providing timely deliveries and strict quality adherence.
Automotive: Driving Innovation
The automotive sector, always at the vanguard of manufacturing innovation, has embraced software solutions wholeheartedly. These systems manage everything from chassis construction to modern vehicles’ intricate electronics. Real-time monitoring ensures that robotic arms weld with precision, while quality control algorithms instantly check components, ensuring they meet stringent standards. With just-in-time production methods, inventory costs are slashed, and efficiency is boosted. Moreover, as electric vehicles gain traction, manufacturing software aids in battery production and management, a critical aspect of this new-age mobility.
Food Processing: Recipe for Efficiency
With its perishable goods and strict health standards, the food industry benefits immensely from manufacturing software. These systems monitor temperature, humidity, and other environmental factors, ensuring optimal conditions for food processing. Automated sorting systems, powered by artificial intelligence segregate produce based on quality. Supply chain systems ensure that products reach their destinations before they perish, and real-time monitoring ensures that any deviation from standards, be it in packaging or processing, is instantly addressed.
Electronics: Circuit of Success
As electronics get more intricate, the need for precision and miniaturization increases. Manufacturing software in this industry aids in everything from silicon wafer production to final device assembly. Quality control mechanisms ensure that each microchip meets the desired performance metrics. Inventory management systems track millions of components, ensuring smooth assembly line operations.
Embracing the Future
The story remains consistent across the board, from steel foundries to pharmaceutical labs. Manufacturing software, emphasising real-time monitoring, production management, and supply chain optimization, has become the linchpin of modern industrial operations. Its ability to boost efficiency, reduce costs, and guarantee quality has made it indispensable.
The move towards business automation isn’t just a trend; it’s a paradigm shift. Industries that adapt and embrace these tools are setting themselves up for success in a world where agility, efficiency, and innovation are not just desired but expected.
How Software Solutions Brings Workflow Automation Efficiency?
Modern manufacturing operations are like a symphony orchestra, with numerous instruments working in harmony to create a cohesive and harmonious outcome. Similarly, in manufacturing, every machine, department, and process needs to function in tandem to produce the desired results. This synchronization, which was once achieved manually, often with its share of hiccups, is today orchestrated with unprecedented efficiency thanks to software solutions. But how exactly do these software tools infuse such seamless efficiency into the workflow? Let’s unravel this.
Integrating Varied Processes:
One of the primary advantages of modern manufacturing software is its ability to integrate various processes. Each step is intricately linked, whether procurement of raw materials, processing, assembling, or dispatching the final goods. Software solutions create an interconnected web where information flows effortlessly from one stage to another. For instance, when a product is assembled, the dispatch department receives real-time notifications, ensuring prompt shipment.
Real-time Monitoring for Instant Decision-Making:
Gone are the days managers had to wait for end-of-day reports to make decisions. With real-time monitoring, every manufacturing process is under constant scrutiny. Any discrepancies, be it a machine malfunction or a drop in production quality, are instantly flagged. This allows immediate interventions, ensuring minor hiccups don’t snowball into significant disruptions.
Asset Management:
A factory is a complex mesh of assets, ranging from heavy machinery to hand tools. Efficient asset management, powered by software solutions, ensures that these tools are always in optimal working condition. Predictive maintenance algorithms analyze wear and tear data to schedule timely maintenance, preventing unexpected breakdowns. Furthermore, asset tracking tools ensure that tools and equipment are readily available when needed, preventing production delays.
Quality Control Automation:
Quality is the cornerstone of any manufacturing operation. With software solutions, quality checks are no longer sporadic and manual. Sophisticated sensors and quality control algorithms continuously monitor the production line. This guarantees a consistent product quality and reduces wastage due to defects.
Resource Allocation and Scheduling:
Manufacturing software solutions come equipped with resource allocation tools. These tools ensure that both human and material resources are used efficiently. Scheduling algorithms allocate tasks based on priority, machine availability, and workforce skills, ensuring minimal downtime and every process runs smoothly.
Enhanced Communication:
One of the overlooked aspects of workflow efficiency is communication. Clear, concise, and timely communication prevents misunderstandings and ensures everyone is aligned towards a common goal. Modern software solutions often come with integrated communication tools, be it instant messaging or task notifications, ensuring that every stakeholder, from the shop floor worker to top management, is on the same page.
What Legacy Software Modernization’s Significance?
In the fast-paced manufacturing world, staying updated isn’t just about keeping up with competitors—it’s about survival. With rapid technological advancements, what was cutting-edge a few years ago might be obsolete today. Legacy software, a relic from a bygone era, often struggles to meet the demands of modern manufacturing processes. But why exactly is modernization so critical? Let’s dive deeper.
Technological Alignment and Integration:
Modern manufacturing processes are complex, relying on various tools, machinery, and systems. These tools often require software that can integrate seamlessly, allowing for fluid data exchange and operations. Legacy systems, designed in an age before the rise of such intricate tools, need help with integration. Modernizing ensures that the software is in alignment with contemporary technologies, allowing for a more harmonious and efficient production environment.
Enhanced Security:
Cybersecurity threats are an ever-looming concern for businesses. Legacy systems, built before the current landscape of sophisticated cyberattacks, often have glaring security vulnerabilities. Modern software solutions prioritize security, coming equipped with robust encryption, regular patch updates, and advanced threat detection mechanisms. Modernizing legacy systems is, therefore, a matter of efficiency and safeguarding critical business data.
Scalability for Future Growth:
Modern businesses must be agile and ready to scale or pivot based on market demands. Legacy software, often rigid in its architecture, can be a bottleneck. Modern solutions, on the other hand, are designed with scalability in mind. Modernized software can adapt without requiring a complete overhaul, whether adding a new production line, integrating a new tool, or expanding to a unique geographical location.
Cost-Efficiency in the Long Run:
While the initial investment in modernizing might seem daunting, legacy systems often have hidden costs. These can range from frequent downtime, manual workarounds, increased training for staff, and potential security breaches. Over time, these costs accumulate, often surpassing the investment required for modernization. By transitioning to modern software, businesses can reduce these ancillary costs, ensuring better profitability eventually.
Improved User Experience:
Legacy systems, with their clunky interfaces and limited functionalities, can be a source of frustration for users. This not only affects morale but can also result in decreased productivity. Modern software, with intuitive interfaces, comprehensive features, and user-friendly designs, enhances the user experience. This makes training more accessible and ensures employees can efficiently execute their tasks.
Leveraging Modern Technologies:
The manufacturing world is witnessing many technological advancements, from the Internet of Things (IoT) to Artificial Intelligence (AI) and Data Analytics. Legacy systems, however, are often incompatible with these modern technologies. Modernizing ensures businesses can leverage these advancements, gaining insights, enhancing automation, and staying ahead of the curve.
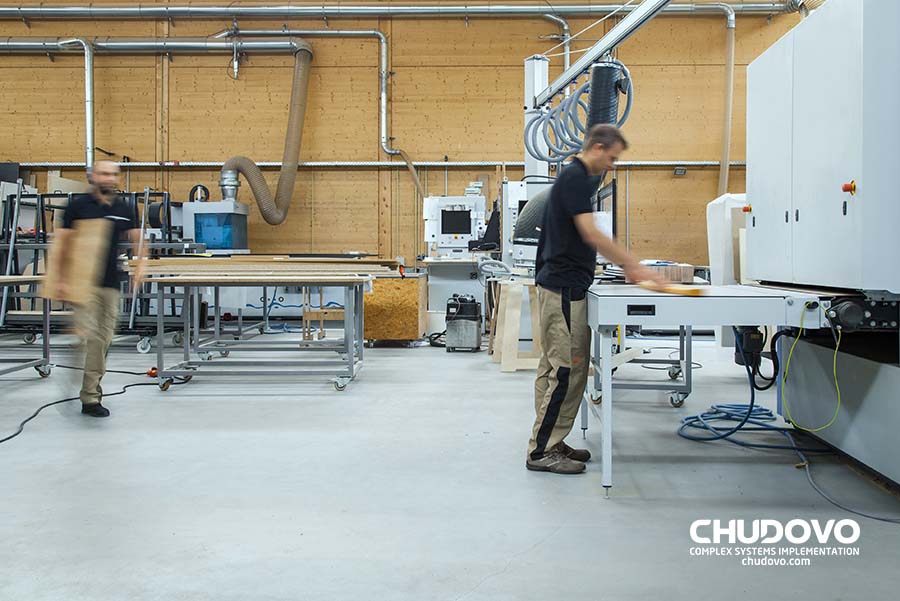
What are Management Benefits from Software Solutions?
In the dynamic manufacturing environment, where markets fluctuate, consumer demands evolve, and production challenges arise, managerial decisions can make the difference between a successful operation and a struggling one. In this context, modern software solutions act as the compass, guiding managers through the labyrinth of variables and uncertainties. Here are the multifaceted benefits that these software solutions offer to management:
1. Instantaneous Insights:
Real-time monitoring ensures that managers are not reviewing outdated reports. Instead, they have access to live data about machine performance, employee productivity, or inventory levels. This instantaneous overview allows for timely interventions, be it ramping up production to meet an unexpected surge in demand or addressing a machine malfunction before it disrupts the entire line.
2. Predictive Analysis:
Beyond just offering a snapshot of the present, modern manufacturing software provides a glimpse into the future. These tools can use sophisticated algorithms and historical data to forecast trends, from potential equipment failures to market demand shifts. Armed with this foresight, managers can preempt challenges, ensuring the operation runs smoothly.
3. Holistic Overview:
Modern software solutions integrate various facets of manufacturing, from supply chain management to production and dispatch. This holistic overview means that managers aren’t just looking at isolated data points but understanding the entire ecosystem. It offers a clearer picture of how changes in one area, say procurement, might affect the rest of the production line.
4. Data-Driven Decisions:
Gone are the days of intuition-driven choices. Today’s managerial decisions are backed by robust data analytics. Whether it’s choosing a supplier, adjusting production schedules, or allocating resources, every choice is grounded in empirical data, ensuring that the decisions are rational, practical, and in line with the company’s goals.
5. Operational Efficiency:
Efficiency isn’t just about speed; it’s about optimizing resources, minimizing wastage, and ensuring the best outcomes. Manufacturing software, with its array of tools, from scheduling algorithms to quality control mechanisms, ensures that operations are streamlined. Managers can thus focus on strategic planning rather than firefighting operational hiccups.
6. Enhanced Communication:
Effective management is often about clear communication. Modern software solutions facilitate this through integrated messaging systems, notification dashboards, or collaborative tools. Managers can seamlessly communicate with teams, suppliers, and other stakeholders, ensuring everyone is aligned with the shared objectives.
7. Strategic Resource Allocation:
One of the challenges managers face is resource allocation. Ensuring optimal allocation is crucial whether it’s workforce, machinery, or materials. With its detailed analytics, manufacturing software provides insights into resource usage, allowing managers to make informed allocation choices for short-term projects or long-term ERP.
8. Risk Management:
Every manufacturing operation is fraught with risks, from supply chain disruptions to machinery malfunctions. Modern software solutions, with their monitoring and predictive capabilities, allow managers to identify these risks early on. This proactive risk management ensures that contingency plans are in place, minimizing potential disruptions.
What is Data Analytics and Business Intelligence?
The manufacturing landscape is awash with data from machinery, employees, supply chains, and end consumers. But raw data, in its unprocessed form, is like an uncut diamond—valuable but not immediately useful. This is where Data Analytics and Business Intelligence come into play, refining this raw data to reveal the gleaming insights beneath.
Data Analytics in Manufacturing:
- Definition:
At its core, Data Analytics in manufacturing involves collecting, processing, and interpreting vast amounts of data generated during production. This can encompass everything from machine telemetry data to sales figures.
- Predictive Maintenance:
Data analytics can predict when a machine is likely to fail or when it might need maintenance. This can significantly reduce unplanned downtimes and boost overall production efficiency.
- Quality Assurance:
Analytics tools can constantly monitor production quality, identify anomalies, and ensure that products adhere to set standards. This reduces wastage and guarantees a consistent product quality for end-users.
- Operational Efficiency:
Through data analytics, inefficiencies in the production line, be it a bottleneck in a particular process or underutilized machinery, can be pinpointed. Managers can then address these issues, ensuring a streamlined production process.
- Supply Chain Optimization:
By analyzing data from suppliers and inventory levels, manufacturing units can optimize their supply chains, ensuring that there’s never an excess or a shortfall of materials.
Business Intelligence in Manufacturing:
- Definition:
While Data Analytics provides insights, Business Intelligence (BI) takes it a step further, converting these insights into actionable strategies. BI tools in manufacturing encompass reporting, querying, dashboards, and more, assisting decision-makers in their strategic planning.
- Decision Support:
With BI, managers get a clearer picture of the production landscape. Whether it’s deciding on a new supplier, expanding a production line, or entering a new market, BI provides the necessary insights to make informed decisions.
- Performance Metrics:
Business Intelligence tools offer a dashboard view of key performance indicators (KPIs), from production efficiency to sales figures. Managers can track these metrics in real-time, ensuring that the operation aligns with the company’s objectives.
- Forecasting:
BI tools can forecast trends, be it potential sales figures based on historical data or anticipated market shifts. This forecasting capability allows manufacturers to preempt market demands, positioning them favorably against competitors.
- Competitive Analysis:
In the competitive manufacturing world, understanding what rivals are doing is crucial. BI tools can provide insights into competitors’ activities, whether their sales strategies, product launches, or marketing campaigns. This intelligence ensures that manufacturers can strategize effectively, staying one step ahead.
How to Conduct Production Planning?
Production planning acts as a roadmap in the complex manufacturing environment, guiding businesses from raw materials to finished goods. It ensures that products are produced efficiently, cost-effectively, and timely delivered to customers. With the aid of manufacturing software, this intricate process becomes streamlined and adaptable. Here’s a breakdown of the key steps involved:
1. Setting Production Goals:
- Objective: Before diving into planning, it’s essential to identify the purpose. Are you looking to maximize production, launch a new product, or optimize current processes?
- How Software Helps: Manufacturing software can store historical data, offer insights into past performance, and help set realistic and ambitious production goals.
2. Evaluating Current Resources:
- Objective: Assess the available resources, including workforce, machinery, and materials. This provides clarity on the production capacity and any limitations.
- How Software Helps: Through real-time monitoring and asset management tools, manufacturing software provides an updated overview of all available resources.
3. Demand Forecasting:
- Objective: Anticipate the demand for the products. This involves analyzing market trends, historical sales data, and external factors like seasonality.
- How Software Helps: Data analytics in manufacturing software can predict demand patterns based on historical data and current market trends.
4. Scheduling Production Runs:
- Objective: Decide when and in what sequence products will be produced. This ensures that machinery is utilized optimally and products are made available as per demand.
- How Software Helps: Advanced scheduling tools in manufacturing software can automatically allocate production runs, considering machine availability, labor, and priority.
5. Inventory Management:
- Objective: Ensure an adequate stock of raw materials and finished goods with sufficient inventory, which can lead to increased holding costs.
- How Software Helps: Inventory management modules in software solutions can track stock levels in real-time and send alerts when replenishment is needed.
6. Quality Assurance:
- Objective: Implement processes to ensure the products meet the set quality standards, leading to customer satisfaction and reduced wastage.
- How Software Helps: Real-time monitoring tools can continuously check product quality, automatically flagging deviations and ensuring consistency.
7. Risk Management:
- Objective: Identify potential bottlenecks, machinery breakdown risks, supply chain disruptions, and other risks that might affect production.
- How Software Helps: Predictive analytics in manufacturing software can foresee potential challenges, allowing for preemptive solutions and contingency planning.
8. Continuous Evaluation and Adjustments:
- Objective: Production planning isn’t a one-time activity. As the market evolves and challenges arise, plans need to be reassessed and adjusted.
- How Software Helps: Business intelligence tools can provide continuous feedback on the production process, allowing managers to make real-time adjustments to the plan.
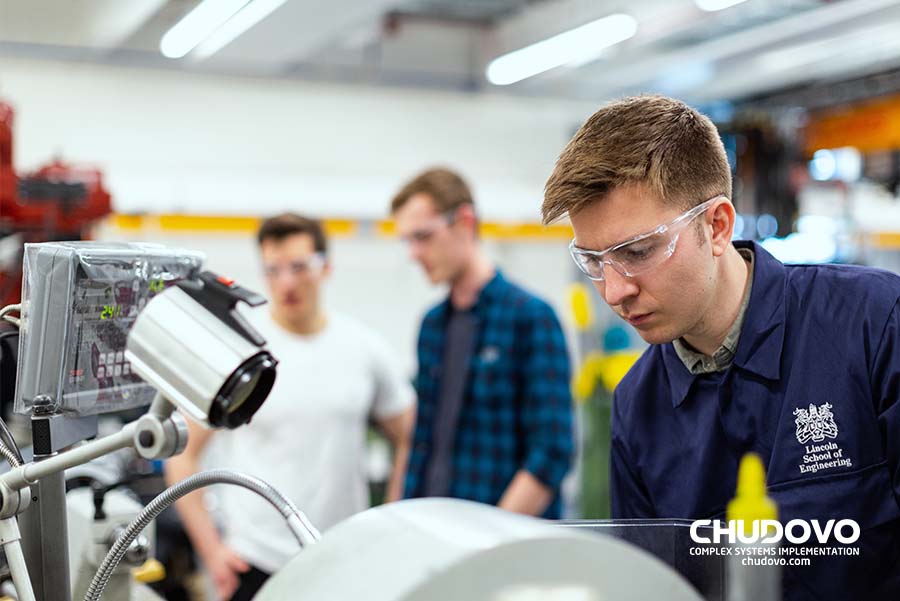
Real-World CHUDOVO Project
Software for Cutting Metal
CHUDOVO developed specialised software for a metal-cutting company. The software integrates with the client’s CNC machines, optimizing cutting processes and ensuring efficient utilization of materials.
Key Features:
- Integration with CNC Machines: The software seamlessly integrates with various CNC machines, allowing for precise control over cutting processes.
- Optimization Algorithms: It uses advanced algorithms to determine the most efficient cutting patterns, minimizing waste and maximizing material usage.
- User-Friendly Interface: With a focus on usability, the software provides an intuitive user interface, ensuring operators can easily configure cutting parameters and monitor operations.
The client could use CHUDOVO’s software to enhance productivity, reduce waste, and achieve significant cost savings in their metal-cutting operations.
Citation:
CHUDOVO. (n.d.). Software for Cutting Metal. Retrieved from https://chudovo.com/projects/software-for-cutting-metal/
Software for Filling Drinks Machines
CHUDOVO designed a software solution for a prominent manufacturer of drink filling machines. The software ensures accurate and efficient filling of beverages into various container sizes.
Key Features:
- Versatile Configuration Options: The software offers flexibility, allowing operators to set parameters for different drink types and container sizes.
- Real-time Monitoring: Operators can monitor the filling process in real-time, ensuring accuracy and consistency.
- Integration with Hardware: It integrates with the client’s hardware setup, providing automated control over the drink filling process.
The client, with CHUDOVO’s software, was able to streamline their drinks filling process, ensuring accuracy, consistency, and efficiency in operations.
Citation:
CHUDOVO. (n.d.). Software for Filling Drinks Machines. Retrieved from https://chudovo.com/projects/software-for-filling-drinks-machines/
Conclusion
In today’s rapidly evolving industrial landscape, the marriage of technology and manufacturing has never been more pivotal. As industries intertwine with digital solutions, businesses have a profound opportunity to redefine their operational capabilities, enhance efficiency, and drive unparalleled growth. Manufacturing Software has emerged as a tool and as the backbone of modern production houses, addressing multifaceted challenges from real-time monitoring to supply chain optimization.
CHUDOVO’s contributions, as evidenced by their innovative projects, underscore the transformative potential of tailored software solutions in reshaping manufacturing paradigms. Whether metal cutting precision or drinks filling accuracy, these software solutions act as catalysts, bridging gaps, enhancing precision, and elevating output.
The message is clear for businesses poised at the brink of decision-making: Embracing modern manufacturing software isn’t just about staying relevant; it’s about leading, innovating, and carving a niche in a hyper-competitive market. As the industrial sector continues its relentless march towards digital transformation, those equipped with the right software solutions will undoubtedly be at the vanguard, setting benchmarks and steering the future of manufacturing. Also, software modernization and its approach to the manufacturing industry have the pivotal role.
FAQ
1. What benefits can Manufacturing Software offer to my business?
Manufacturing Software streamlines and optimizes the production process by offering real-time monitoring, data analytics, and business intelligence. These features can increase production efficiency, reduce costs, improve quality control, and better asset management. In addition, modern manufacturing software can assist in supply chain optimization, legacy software modernization, and overall business automation, ensuring businesses stay competitive in today’s fast-paced industrial landscape.
2. How has CHUDOVO contributed to the advancement of manufacturing operations with its software solutions?
CHUDOVO has developed specialized software solutions tailored to specific manufacturing needs. For example, they created software for metal-cutting companies that integrates with CNC machines, optimizing cutting processes and ensuring efficient material utilization. Another project involved designing software for a drinks-filling machine manufacturer, providing precise and efficient drink filling for various container sizes. These real-world implementations demonstrate CHUDOVO’s commitment to enhancing industrial processes through innovative software solutions.
3. Why is Legacy Software Modernization crucial for manufacturing businesses?
While legacy software systems may have been influential in the past, they can become outdated and inefficient over time. Relying on such systems can hinder production efficiency, lead to compatibility issues, and pose security risks. Modernizing legacy software ensures businesses have access to the latest technological advancements, better security, and scalability, enabling them to adapt to evolving market demands and stay ahead of competitors.